3D Printed Molds for Fiberglass Wrapped Structural Nodes
2022

This line of research explores alternative mold-making for structural fiberglass composite parts. Traditional molds or tooling are expensive to construct and often necessitates an economy of scale in production. With the need for variation part to part, the introduction of 3D printing—as a means of rapidly constructing unique and geometrically specific molds— allows for the manufacturing of non-standard or repetitive structural fiberglass composites.
The research explores the use of FFF 3D printing with bio-plastic PLA filament to construct the molds for composite parts. This process results in molds that are inexpensive and sustainable to produce. The mold is left in place during the lamination process but is not structural on its own. Only through the wrapping and lamination of the fiberglass tape, do the parts become structural. The process for lamination used 1” and 2” tape to accommodate the curvature and to sufficiently cover the surface of the molds. The fiberglass was wet out with a bio-resin matrix, which further reduces the environmental impact of the composite construction.
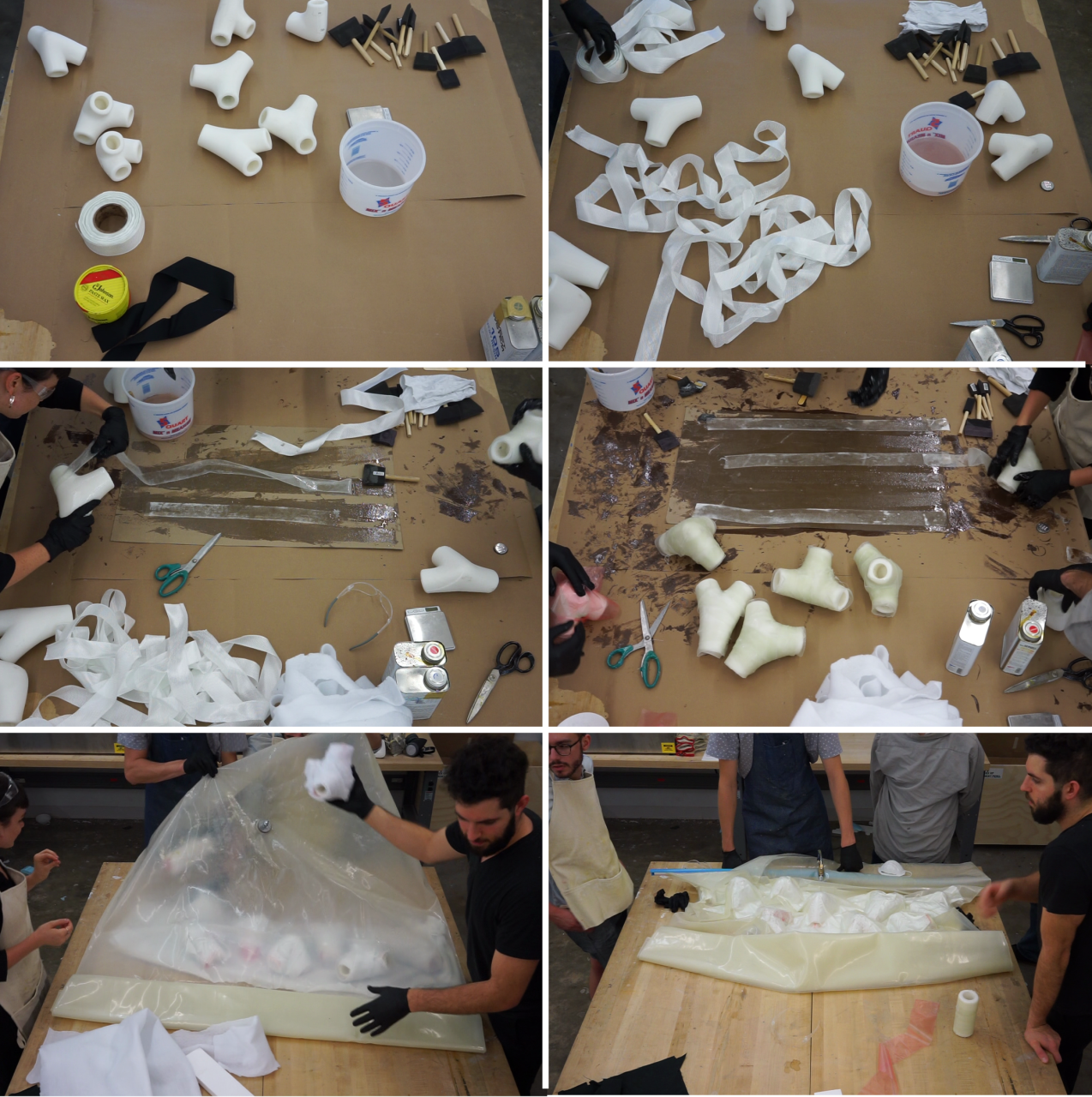
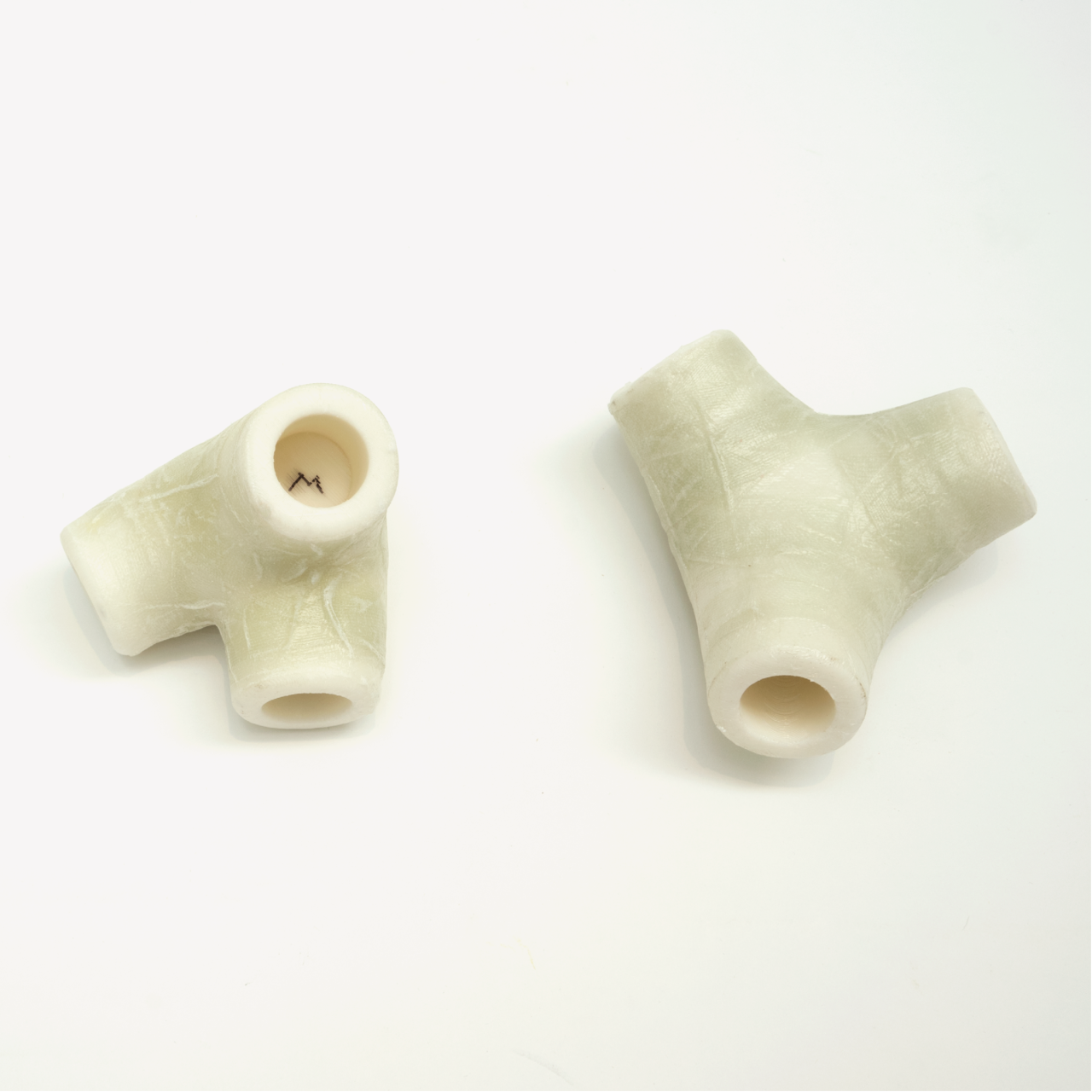
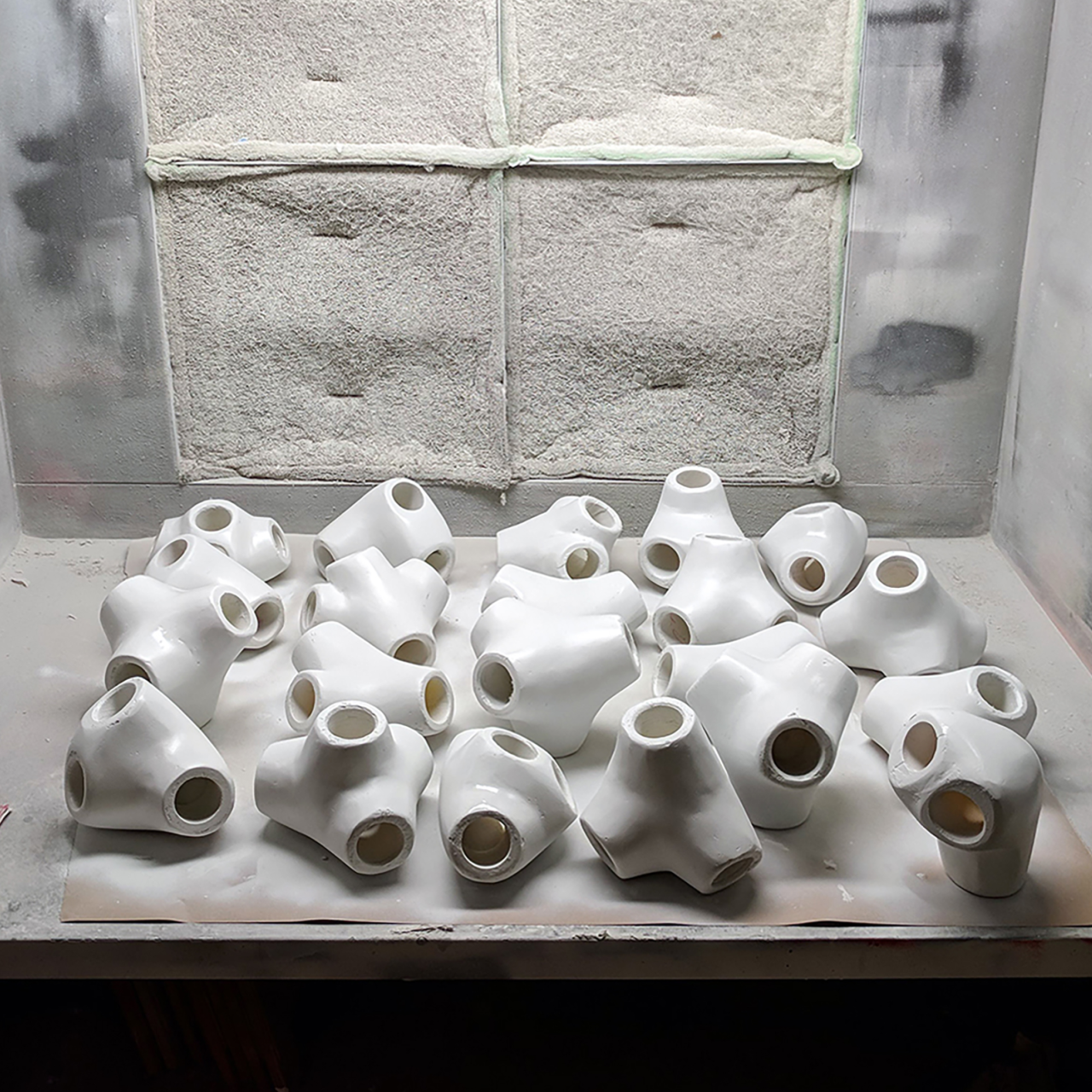
The resulting structural parts are used in conjunction with off-the-shelf, pultruded fiberglass tubes to construct an interactive urban play structure. The structural nodes and the pultruded tubes are adhered with epoxy resin, allowing for a simple and rapid final assembly. This structure then serves as the frame for two woven surfaces, allowing the object to be occupied sectionally. Twisted 1/2” polypropylene marine-grade rope is used to construct a soft interface, producing a playful, energetic, woven urban object, that allows people to climb, sit, and engage.
The design of the play structure—titled TipTap—utilizes the variation allotted by the manufacturing process to create a dynamic and engaging installation. The design of the object is conceived of as two offset circles. The outer circle is 15’ in diameter, and the inner circle is 5’ in diameter. Each circle is segmented into seven equal parts to allow construction using linear structural members. The resultant heptagons are strategically shifted from the initial center points producing varied experiences and interactions with the urban object. The spacing on one side of the object allows for people to lay horizontally in a hammock-like condition. On the opposite side, the distance is reduced, directing the user upright into a seated position.
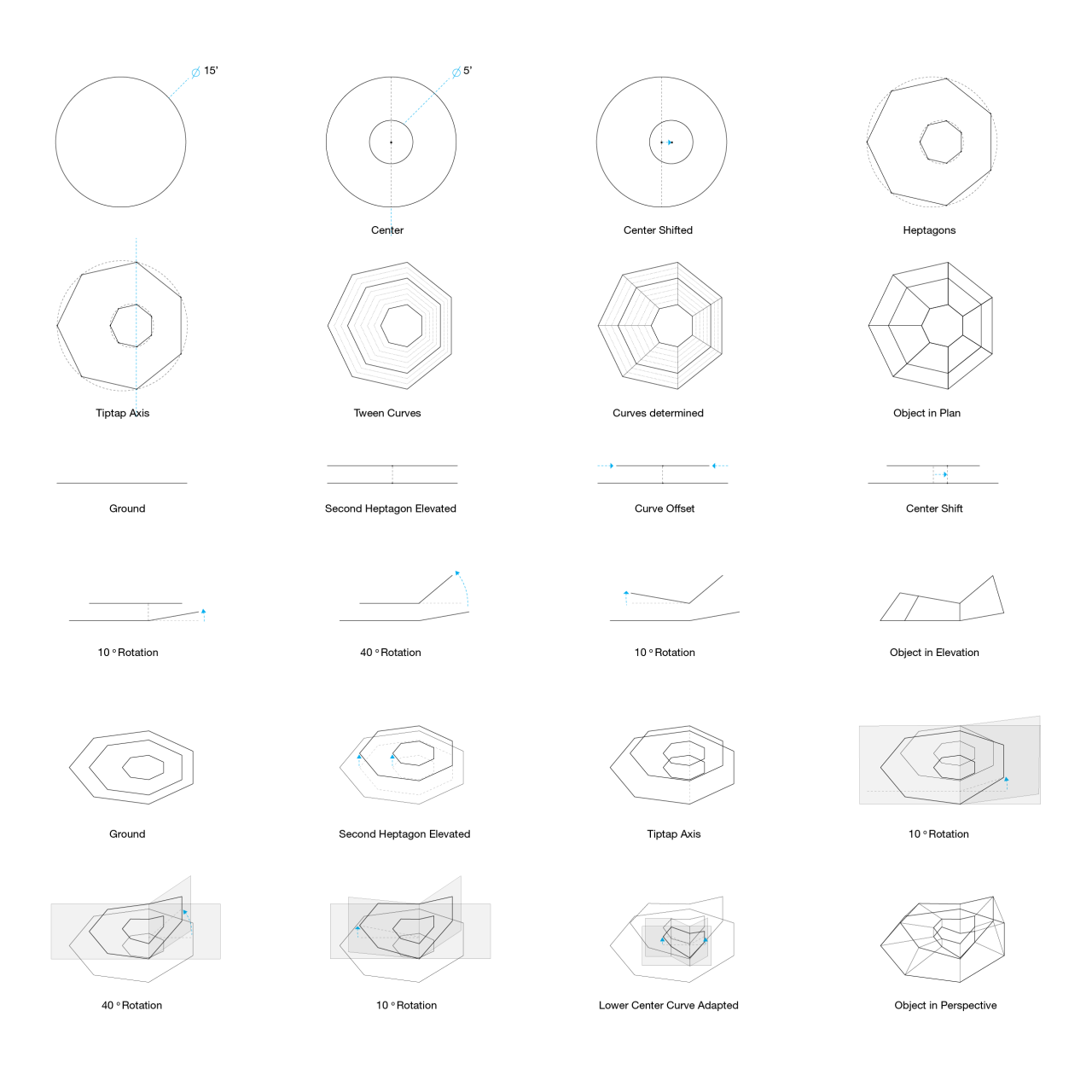
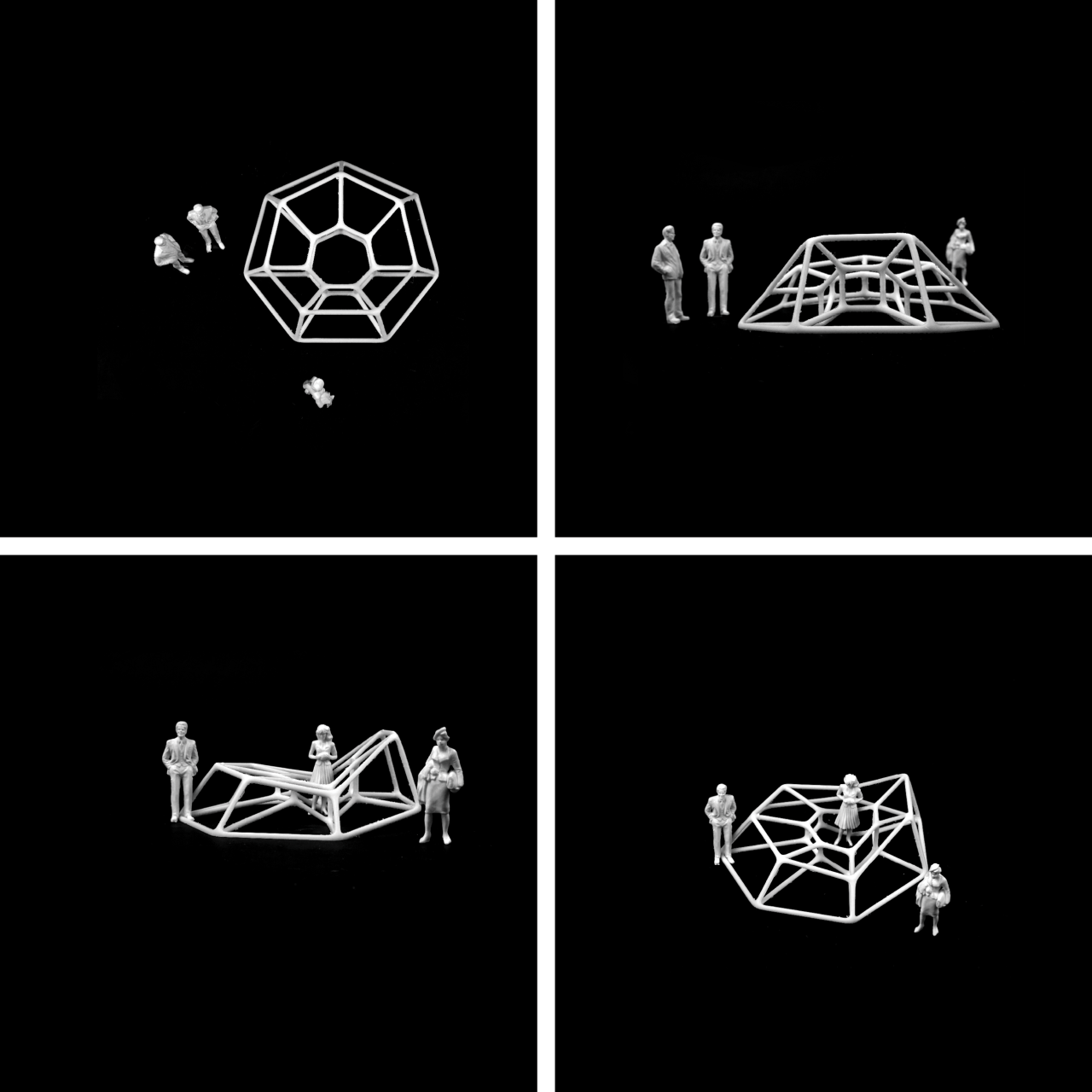
This varied experience of occupation is heightened through a larger scale of interaction. Two vertices from the larger heptagon are strategically aligned with two vertices from the smaller, shifted heptagon producing a tipping axis. On the narrow ‘upright’ portion of the object, the geometry is slightly lifted from the ground plane allowing the entire object to teeter back and forth depending on occupation. The small seesaw-like interaction activates the object more broadly and encourages user movement, climb, and play.
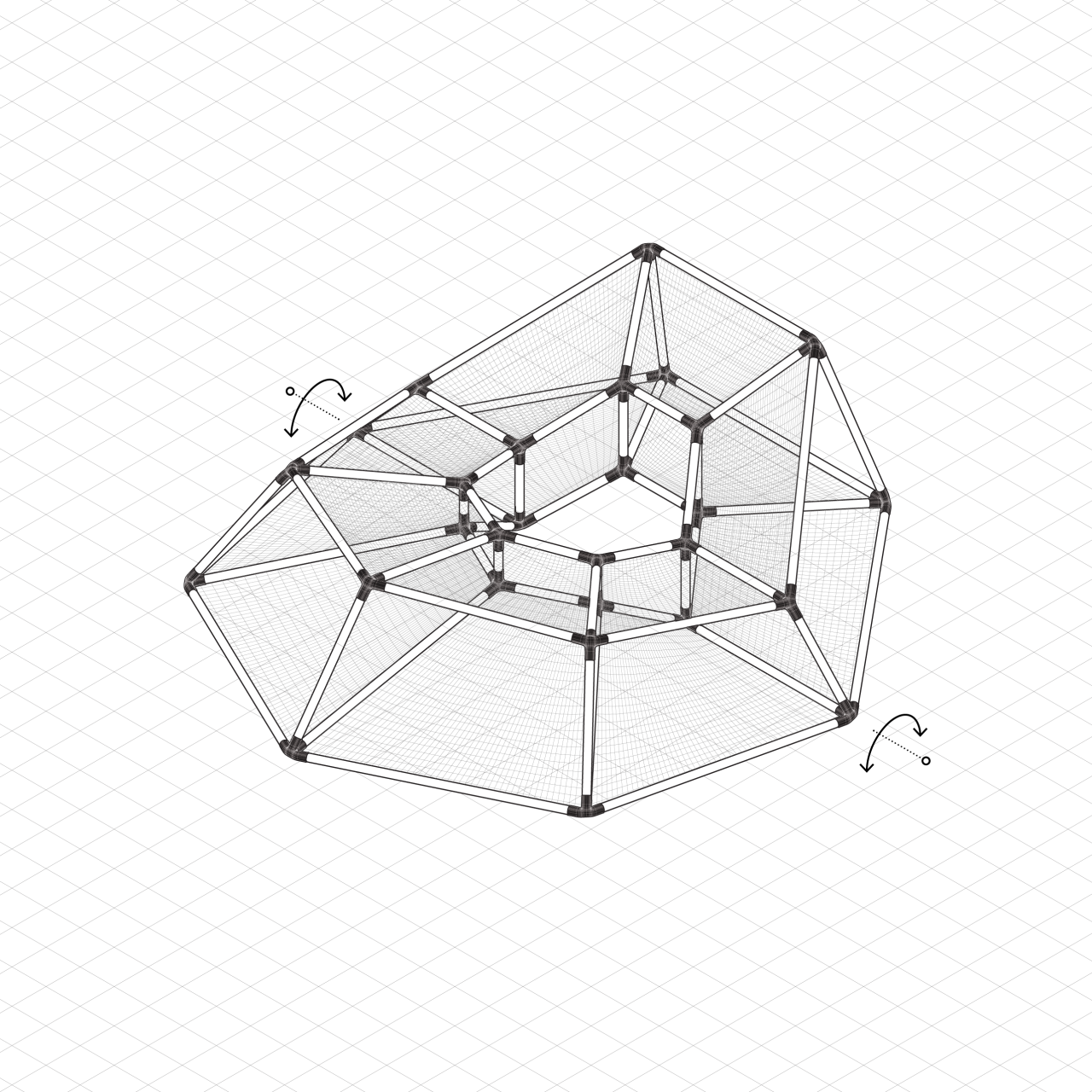
Keywords—
3D Printing, Fiberglass Reinforcement, Material Research, Digital Manufacturing
Topics—
Emerging technologies, Steel and composite structures
References—
XYZ
Illustrations—
XYZ
News—
https://re3d.org/rice/
https://lawndaleartcenter.org/exhibition/david-costanza-tip-tap/
https://bustler.net/news/7209/a-series-of-teetering-beds-has-been-announced-as-the-winningproposal-of-the-2019-ragdale-ring-competition